轻量化是汽车长期趋势,新能源里程焦虑加速轻量化发展
2020 年 10 月,中国汽车工程学会牵头组织编制的《节能与新能源汽车技术路线图 2.0》发布,对各种类型的汽车每百公里油耗提出了要求,预计在 2030 年,我国新能源汽车占到总销量 40%,乘用车百公里油耗达 3.2L,响应“双碳”目标。从燃油车角度来看,汽车的平均油耗与整车质量呈正相关,汽车轻量化对于降低传统车油耗具有积极促进作用。根据研究,汽车重量每减轻 10%,最多可实现节油 5-10%;汽车整备质量每减少 100 千克,百公里油耗可降低 0.3-0.6 升。
近几年,我国新能源汽车渗透率持续走高,但“里程焦虑”仍限制消费者购买新能源汽车。一般来说,传统燃油车加满油可以行驶 500 公里以上,而大部分电动车的续航里程在 300-500 公里左右,仍然存在差距。
新能源汽车解决里程焦虑包括以下方式:
(1)提升电池能力密度。《我国制造 2025》明确了动力锂电池的展开规划:2020 年,电池能量密度抵达 300Wh/kg;2025 年,电池能量密度抵达400Wh/kg;2030 年,电池能量密度抵达 500Wh/kg。
(2)增加电池组数量并减重。与传统能源汽车相比,新能源汽车由于搭载三电系统,往往比燃油车重 10%,增加电池组数量可提升续航里程,但是电池组总重达 900Kg,已占总车质量的 42.7%。因此,可以看到提升续航里程中很重要的一个方式就是汽车减重。
汽车轻量化是汽车工业发展的大趋势,轻量化实现路径主要包括材料、工艺、结构三个方面,可从动力、车身、底盘、内外饰等多个部位减重。
根据观研报告网发布的《中国汽车轻量化行业发展趋势分析与投资前景预测报告(2023-2030年)》显示,目前来看,车企轻量化方向包括:1)在汽车底盘、动力、车身、电池盒等部件上用铝合金代替钢;2)内外饰件使用塑料代替钢;3)使用一体化压铸工艺。汽车零部件每个环节都能实现轻量化制造,国内外主流零部件公司均在致力于轻量化制造。
汽车轻量化的可实现零部件方向
资料来源:公开资料整理
铝合金、镁合金等是汽车轻量化的关键材料。
1、铝合金
铝合金是现阶段较好的轻量化材料之一。当前众多主流车型均采用全铝车身,前后悬架大部分材料也采用铝合金,用铝化程度越来越高,最大程度实现轻量化制造。
目前底盘、车身、刹车系统等用铝转化比率较低,未来十年内汽车的多个主要部件用铝渗透率都将明显提高。工信部《节能与新能源技术路线图》提出我国 2025/2030 年单车用铝量目标为250kg/辆和 350kg/辆,2030 年单车铝合金用量相较于 2021 年有望翻倍增长。
汽车各部位用铝量(kg)
部位 | 2018年 | 2025年E | 2030年E |
底盘和悬架 | 11.6 | 39.5 | 59.4 |
轮毂和刹车系统 | 24.6 | 44.7 | 49.7 |
电池系统 | 42.2 | 53.3 | 59.3 |
传动系统 | 9.8 | 17.4 | 19.4 |
热交换系统 | 11.1 | 14.9 | 16.6 |
车身结构 | 9.9 | 18.5 | 25.3 |
车身开闭件 | 8 | 23.3 | 36.3 |
碰撞管理系统 | 6.9 | 9.4 | 11.1 |
其他部件 | 4.4 | 5.8 | 6.4 |
合计 | 128.5 | 226.8 | 283.5 |
资料来源:工信部,公开资料整理
2、镁合金
镁合金有着减震等独特的优势:1)密度较低但强度高,在主要金属中,镁的密度相较于铝降低 35%,是目前商用最轻的金属结构材料;2)韧性好、阻尼衰减能力强,可以有效减少振动和噪声;3)热容量低、凝固速度快,压铸性能好;4)具有优异的切削加工性能;5)资源丰富且易于回收再生。综上,镁合金可满足军民多领域对轻质、高强、抗冲击、防辐射等要求,目前镁合金压铸工艺处于高速成长阶段。
镁合金压铸处于高速成长期
资料来源:公开资料整理
据《节能与新能源汽车技术路线图 2.0》规划,未来 10 年汽车轻量化发展趋势不变,铝、镁等轻量化材料在车身的应用比例有望不断上升。2020 年、2025 年、2030 年,单车用镁量计划达到15kg、25kg、45kg,镁合金整车占比分别为 1.2%、2%、4%,发展空间广阔。
资料来源:工信部,招股说明书,观研天下数据中心整理
一体化压铸是轻量化的前沿技术,先发企业将构筑高壁垒
传统汽车生产制造由冲压、焊装、涂装、总装四大工艺组成。其中,冲压就是将金属板材压制成车身所需的各个组成部件,而后再采用焊接或铆接组合的方式制造出大型铝制件。而一体化压铸则是采用特大吨位压铸机,把冲压与焊装改为压铸,前两步合成一步,将多个单独、分散的零部件高度集成,直接铸造出大部件。
汽车一体化压铸的优势
资料来源:公开资料整理
一体化压铸有两种业务模式,一种是自研模式:主机厂直接采购压铸机、材料和模具等物料,自建工厂生产压铸件,代表车企有特斯拉、小鹏和沃尔沃。另一种为采购模式:主机厂直接向压铸厂商采购压铸件,由压铸厂商采购相关的物料,生产压铸件后交付给主机厂,代表车企有蔚来、理想。长期来看,由于主机厂自建厂房与产线成本较高,并且汽车销量可能会成为产能利用率的压制因素,因此采购模式有望成为长期主流。
从产业链来看,一体化压铸产业链的上游为压铸机、材料与模具厂商,中游为铝合金压铸厂和自研主机厂,下游为采购主机厂。
一体化压铸产业链结构
资料来源:公开资料整理
从进入壁垒来看,一体化压铸也有着较高的技术壁垒,使得厂商先发优势会被放大。
1、材料壁垒
材料配方和专利为免热处理铝合金的核心竞争壁垒,构筑产业有较高的客户粘性和进入门槛。免热处理铝合金的设计思路是以铝为基础金属元素,控制硅、镁、铁、铜、锰、锌等元素的含量和配比关系,不同合金元素的加入会直接影响铝合金的机械性能。对于一体化压铸件来说,铝合金的机械性能要求更高,复杂的材料配方大幅提升了厂商进入一体化压铸市场的技术门槛,已掌握合金原料配方和专利的企业更具优势。同时材料的专利会锁定铝合金材料配方,包括重要元素的种类和含量,也为材料厂商的重要竞争点。
免热处理铝合金是一体化压铸的重要环节,涉及零件、模具设计以及后续工艺优化等环节,为避免专利纠纷,整车厂一般会指定材料厂商,并更倾向于选择有专利保护的厂商,因此材料专利一般为主机厂与材料厂商合作的前提。同时已授权专利厂商会对新进入者形成较大阻碍,后来者即使在现有专利基础上进行元素微调也可能属于专利侵权。
2、设备壁垒
(1)高技术门槛
一体化压铸件对压铸设备的锁模力提出更高的新要求,由于压铸机的锁模单元需要提供足够的锁模力以确保合金溶液注入模具时模具不被撑开,因此越大型的压铸机要求越大的锁模力。特斯拉布局一体化压铸之前,业内压铸机最大锁模力在 4400 吨,而压铸机的锁模力每提升 500 吨一般需要 1-2 年,有较大吨位的压铸机厂商更有先发优势。同时,由于一体化压铸件为多个零部件压铸而成,降低了汽车零部件的通用性,压铸设备需主机厂与压铸商定制开发,如特斯拉与全球知名压铸厂商 IDRA Group 合作开发大型一体化压铸机 Giga Press。压铸设备的高度定制化属性使得产业有较高的定制开发技术壁垒。
(2)高资金储备要求
主机厂布局一体化压铸需设立压铸岛,其由压铸机、模具、其他周边配合设备构成,具有较高的价值量,同时由于一体化压铸技术对压铸机性能要求较高,有较高的研发成本,根据力劲集团的公告,其研发大吨位压铸设备的设备投入约 8000 万元资本能力为压铸设备产业的重要竞争壁垒,且要求厂商有能力规模化生产以分摊较高投资成本。
在主机厂纷纷跟进布局一体化压铸的需求驱动下,压铸机大型化发展趋势基本确立,5000 吨以上的锁模能力有望成为厂商的重要竞争要素。目前力劲集团在 5000 吨以上机型市场先发优势明显,同时国内外压铸机厂商纷纷加快布局,布勒 2023 年下线了 9200 吨压铸机,海天金属推出了 8800 吨机型,伊之密推出了 9000 吨机型。
3、模具壁垒
压铸技术是一种通过将铝液在高速高压下射入紧缩的模具空腔内结晶凝固的方法来生产铝合金件的工艺。压铸工程中模具的可靠性对于压铸件的良品率至关重要,具体而言,压铸模具的质量决定了铸件的形状和尺寸公差级别,浇注系统决定了金属液的填充情况,而模具的强度限制则决定了最大压射比压等。随着压铸模具的不断升级,模具的制造难度也在逐渐增加。模具的精度越高,就需要更复杂的热平衡设计、更高难度的机械加工和更多的脱模设计考虑因素,技术难度也就越大。
由于当前超大型模具技术壁垒较高,较少模具厂商具有超大型一体化模具生产能力,近乎所有 Tier1 厂商采用外购模具模式,因此当前模具市场呈现高端缺乏、低端竞争激烈的格局,同时大型一体模具市场的集中度更高,目前我国中高端模具厂商主要有赛维达、广东型腔、臻至等,旭升股份从模具起家,也具有模具设计能力,在2022 年 10 月战略投资科佳模架后,模具设计能跟市面上的大型压铸机的吨位进行匹配。一体化压铸件需要设备、模具、材料等产业配合,要求极强的产业 know-how积累,其中模具结构复杂、大型化生产能力稀缺、且具有强定制化水平,大型压铸模具市场有更强的竞争壁垒,当前模具厂商与 Tier1 合作为主要商业模式,头部有望受益产业链扩张,得以迅速成长。
4、生产经验壁垒
实际压铸过程面临复杂多变的作业环境,模拟仿真分析或有效补充第三方压铸厂的工艺 know-how 能力。压铸前进行的仿真模拟分析可充分预测压铸过程中可能发生的缺陷,并对工艺设计做出相应改良措施,有望提高产品良品率、加快生产节拍。一体化压铸产业方兴未艾,压铸厂对大型一体化压铸件的工艺积累尚且不足,往后看,具备强大软件分析能力的压铸厂可结合模拟仿真结果与实际工艺经验,有望快速补充行业 know-how 短板,调整到相对最优的工艺参数。
第三方压铸厂前期固定资产布局包括厂房和大吨位压铸机,一方面一体化压铸厂房一般需较大面积满足较高的生产需求,一方面大吨位压铸机单机价值量较高,导致整体资金投入水平较高。同时由于一体压铸结构件尺寸和重量较大,运输成本较高,压铸厂一般需要在主机厂附近建厂就近供货,以快速响应主机厂需求、降低运输成本。抢占了产能布局先机的厂商有望在中短期内维持竞争优势,可凭借现有或规划产能获得更多订单,率先享受产业发展红利。(YM)
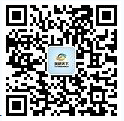
【版权提示】观研报告网倡导尊重与保护知识产权。未经许可,任何人不得复制、转载、或以其他方式使用本网站的内容。如发现本站文章存在版权问题,烦请提供版权疑问、身份证明、版权证明、联系方式等发邮件至kf@chinabaogao.com,我们将及时沟通与处理。